
86 17344894490
service@chalcoaluminum.com
- Forges en aluminium pour véhicules ferroviaires
- Feuille de plaque d’aluminium pour les véhicules ferroviaires
- Profil en aluminium pour les véhicules ferroviaires
Quel aluminium est utilisé pour fabriquer le train
L’allègement des véhicules ferroviaires, en particulier l’allègement des voitures de voyageurs à grande vitesse et à deux étages et des rames de métro, est la question centrale de la modernisation du transport ferroviaire, et le moyen le plus efficace d’améliorer l’allègement des véhicules est d’utiliser un grand nombre de matériaux en alliage d’aluminium. Par conséquent, comment améliorer le degré d’aluminisation des véhicules est devenu une tâche très importante pour la conception de véhicules, les experts en fabrication et les experts en matériaux.
Dès 1986, la Français National Railway Corporation a utilisé pour la première fois des matériaux en alliage d’aluminium sur les cadres de fenêtres des wagons de voyageurs. En 1905, le Royaume-Uni a également utilisé l’alliage d’aluminium pour fabriquer les panneaux muraux extérieurs et les matériaux de décoration intérieure des voitures électriques de chemin de fer. Depuis 1905, les États-Unis utilisent l’alliage d’aluminium pour fabriquer des portes et des fenêtres, des toits, des panneaux muraux extérieurs, des tuyaux de paroi intérieure, des bogies, des noyaux de roues et des matériaux décoratifs de voitures électriques et de voitures particulières à grande échelle. Depuis lors, il s’est rapidement étendu à l’Italie, à l’Allemagne, à la Suisse, au Canada et à d’autres pays.
En 1962, le chemin de fer électrique japonais Shanyang a adopté pour la première fois la voiture à structure entièrement en aluminium, qui est devenue le centre d’attention de tous les pays du monde. La technologie de fabrication des véhicules ferroviaires en alliage d’aluminium au Japon s’est développée rapidement. À l’heure actuelle, les véhicules en alliage d’aluminium ont été utilisés dans 54 types de véhicules de 19 unités d’exploitation tels que les chemins de fer nationaux, les chemins de fer privés, les chemins de fer Shinkansen et le métro. La méthode d’assemblage de tous les véhicules en aluminium est passée du processus traditionnel de revêtement de plaques minces sur le squelette à une nouvelle méthode d’assemblage de pièces extrudées à grande échelle avec les plaques extérieures du squelette.
Avec le développement rapide de l’économie nationale et l’amélioration continue du niveau de la science et de la technologie, des besoins de plus en plus urgents sont mis en avant pour la légèreté du transport ferroviaire, ce qui favorise grandement le processus de tout l’aluminium des véhicules ferroviaires et des voitures de passagers à deux étages à grande vitesse. Ces dernières années, en particulier depuis l’approfondissement de la réforme et de l’ouverture,
En plus d’introduire des technologies de conception et de fabrication avancées de tous les véhicules à structure en aluminium et des véhicules de métro en alliage d’aluminium léger de l’étranger, la Chine organise des collèges et des universités, des instituts de recherche scientifique et des usines pour développer des voitures de tourisme à grande vitesse, des voitures de tourisme à deux étages et des véhicules de métro, et a réalisé des réalisations importantes. On peut s’attendre à ce qu’avec le développement de l’industrie chinoise des transports, en particulier le développement des chemins de fer à grande vitesse, des véhicules ferroviaires à double couche et du transport par métro, une large route soit ouverte pour le développement et l’application de l’aluminium dans l’industrie des transports.
Application spécifique de l’alliage d’aluminium dans la structure de carrosserie des voitures: la première production en lot de véhicules à structure en aluminium a été le tramway du métro de Londres en 1952. En 1962, le tramway en aluminium de 2000 du chemin de fer électrique de Shanyang est apparu au Japon. Depuis lors, le chemin de fer électrique de Shanyang, le chemin de fer d’État et le chemin de fer privé ont tous rivalisé pour utiliser des véhicules en alliage d’aluminium. Dans les années 1980, il y avait 40 types de véhicules à structure en aluminium au Japon, avec plus de 4000 véhicules. À l’heure actuelle, il existe plus de 5000 véhicules à structure en aluminium dans le monde. Ces véhicules utilisent pleinement les caractéristiques d’origine de l’alliage d’aluminium: poids léger, haute résistance, bonne aptitude au traitement, soudabilité, résistance à la corrosion, belle apparence, etc. tandis que la taille de base, la forme et la méthode de fabrication sont toutes conformes aux véhicules à structure en acier traditionnels. Le principal inconvénient de ce véhicule à structure en aluminium est que la rigidité diminue proportionnellement à la réduction de poids.
Afin de s’adapter au chemin de fer à grande vitesse, de réduire le changement de pression dans le tunnel et d’éviter les vibrations du centre passagers, le véhicule à structure fixe, c’est-à-dire le corps de structure en alliage d’aluminium du Shinkansen japonais 2000, est développé. Par rapport au véhicule traditionnel, sa taille est presque similaire, mais sa configuration est complètement différente. Tirant parti des caractéristiques de haute résistance spécifique et de bonne aptitude au traitement de l’alliage d’aluminium, les éléments structurels sont disposés aux extrémités supérieure et inférieure de la structure latérale pour maintenir la même rigidité et réduire son poids.
Le développement de matériaux en alliage d’aluminium et de grands profilés extrudés ouvre la voie à la modernisation structurelle et à la légèreté des véhicules ferroviaires, et la modernisation structurelle et la légèreté des véhicules ferroviaires soulèvent de nouveaux problèmes et augmentent la puissance pour le développement et l’application de matériaux en aluminium. En termes de matériaux, les véhicules ferroviaires ont des exigences élevées en matière de propriétés mécaniques, de formabilité de traitement, de résistance à la corrosion, de résistance à la fatigue et de performance de soudage. Par conséquent, en fonction des différents composants, des différentes utilisations et des différentes pièces, les alliages de la série 5000 (tels que 5005, 5052, 5083, etc.), des séries 6000 (telles que 6061, 6n01, 6005A, 6082, 6063, etc.) et des séries 7000 (telles que 7N01, 7003, 7005, etc.) doivent être sélectionnés.
Des années 1950 aux années 1960, les véhicules ferroviaires étaient généralement assemblés et soudés avec un panneau extérieur en alliage 5083, un squelette et une plate-forme 7N01. Cependant, ces dernières années, en raison des exigences de la normalisation à grande échelle (double couche), à grande vitesse et légère et de la construction et de l’entretien simplifiés des véhicules ferroviaires, ainsi que du développement réussi de panneaux muraux intégrés à grande échelle et de profilés creux complexes à paroi mince, l’application de profilés extrudés à grande échelle sur les véhicules ferroviaires a été encouragée. Les profilés complexes à paroi mince utilisés dans les panneaux muraux intégraux à grande échelle et les sections creuses des véhicules ferroviaires sont produits sur les extrudeuses à grande échelle ci-dessus. Cette grande extrudeuse, équipée de cylindres d’extrusion plats, peut produire des profilés creux poreux complexes à paroi mince d’une largeur de 600 mm, d’une hauteur de 60 mm, d’une épaisseur de 3 mm et d’une longueur de plus de 20 mm.
Ces profilés extrudés de précision intégrale à grande échelle sont assemblés par soudage par points par résistance et soudage à l’arc blindé au gaz inerte, ce qui permet d’économiser considérablement des heures de travail et de réduire le poids. De plus, la rigidité globale, la rigidité locale et la résistance à la fatigue des pièces soudées sont équivalentes à celles des structures en acier.
Par conséquent, ce matériau structurel en aluminium idéal crée des conditions favorables à la modernisation des véhicules ferroviaires
Application de matériaux en aluminium dans d’autres parties que la carrosserie
En 1975, le Japon a utilisé des profilés extrudés à grande échelle pour fabriquer les poutres de support de la carrosserie et de la plate-forme Workshop sur les véhicules de type Shinkansen 200. Il réalise des réalisations remarquables dans le poids léger des pièces de chariot.
Les jantes en alliage d’aluminium sont appliquées sur la plaque centrale des roues des véhicules ferroviaires le long de la côte de la baie de Fulangsi aux États-Unis, ce qui réduit considérablement le poids du véhicule. Dans d’autres applications, il existe des boîtes de roulement en alliage d’aluminium, des boîtes de vitesses, des cadres d’essieux de cadre et des bielles entre la carrosserie de la voiture et le chariot. En raison de la légèreté, le poids de chaque boîte de roulement est réduit de 73 kg à 28 kg. En outre, sur les véhicules ferroviaires de type tampon magnétique mlu001 et mlu002, le panneau extérieur est en aluminium dur, le cadre arrière est en aluminium 7N01, la fente extérieure de l’électromagnétisme supraconducteur est également en alliage d’aluminium structurel 5083 et en alliage 1100 à faible résistance, et les bobines de gaz électriques pour les coussinets magnétiques et la propulsion de guidage sont toutes en alliage d’aluminium, L’échangeur de chaleur du congélateur liquéfiant l’hélium, qui joue un rôle important dans la supraconductivité, est constitué de panneaux muraux creux en alliage d’aluminium poreux.
Il existe de nombreux types de pièces en alliage d’aluminium utilisées dans le véhicule et le poids total est considérable. Tels que 471 kg de pièces de décoration intérieure, 153 kg de plaques décoratives, 334 kg de portes et fenêtres, 153 kg de pièces d’équipement intérieur, 190 kg de conduits de ventilation et d’amortisseurs et 254 kg de dispositifs de contrôle.
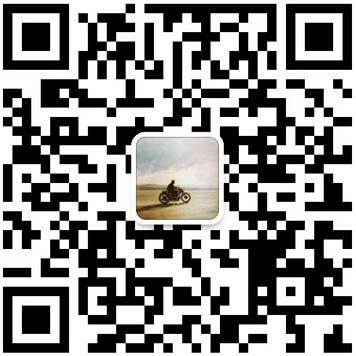
Offre gratuite de produits, bienvenue à consulter à tout moment, nous donnerons la première réponse. Notre e-mail: