
86 17344894490
service@chalcoaluminum.com
- Forges en aluminium pour véhicules ferroviaires
- Feuille de plaque d’aluminium pour les véhicules ferroviaires
- Profil en aluminium pour les véhicules ferroviaires
Pièces structurelles de profilés en aluminium extrudé dans la fabrication de véhicules
Selon les informations, environ 60% des commandes existantes des constructeurs européens de locomotives et de véhicules sont des véhicules avec une carrosserie en aluminium. Il y a 20 ans, ces commandes n’étaient que de 2% à 3%. Maintenant, la structure en aluminium a été appliquée dans la glace, tgv-2n, etr460, etr500, le train Talgo Hotel et d’autres trains à grande vitesse, ainsi que de nombreux véhicules de transport ferroviaire suburbain et urbain.
L’adoption de pièces structurelles en profilés d’aluminium extrudé a commencé au début des années 1970. À cette époque, les progrès scientifiques et technologiques dans l’application des profilés en aluminium avaient permis de fabriquer des composants en aluminium selon la forme et la taille requises. Ce composant en aluminium a été appliqué à la carrosserie basculante des trains apt en Grande-Bretagne. Cependant, à cette époque, l’application de composants en aluminium extrudé ne produisait pas de grands avantages, c’est-à-dire que les prix plus élevés des matériaux n’étaient pas compensés par la réduction de la charge de travail de fabrication. À cette époque, l’utilisation de pièces structurelles de grande taille ne réduisait la charge de travail de production de la carrosserie que de 40% et réduisait le poids mort de la carrosserie de 26 m de long à 7,5 t, tandis que le poids mort de la carrosserie en acier de 26 m de long était de 11 T. Dans les années 1970, le département ferroviaire a accordé plus d’attention au calcul du coût total de toute la durée de vie des véhicules (coût d’achat plus coût d’exploitation et d’entretien). Ils se sont rendu compte que la consommation d’énergie de traction des trains doit être maintenue au même niveau, qui dépend en grande partie du poids propre du matériel roulant.
Plus tard, certaines nouvelles mesures techniques et technologiques, dont la plus importante a été réalisée au milieu des années 1980, telles que l’adoption de la méthode d’extrusion de pièces structurelles de grande taille de coque à double couche, qui a réduit au minimum le besoin de fixations transversales, ont encore réduit le temps de production de la carrosserie en aluminium du véhicule, réduit de 50% par rapport aux véhicules en acier, et il a été possible de fabriquer un corps de cylindre à double couche selon la méthode conventionnelle, puis l’ouverture des trous de fenêtre Les opérations de soudage sont toutes réalisées dans le processus d’opérations techniques unifiées, en utilisant seulement partiellement la technologie et l’équipement robotisés.
Aujourd’hui, lorsque les départements ferroviaires réduisent progressivement et de plus en plus leur participation au développement de nouveaux véhicules et mettent en œuvre des politiques d’achat afin de réduire les coûts de fabrication initiaux et les dépenses d’exploitation futures, les fabricants ont une plus grande liberté dans l’adoption de nouvelles structures et de nouveaux matériaux pour répondre aux exigences techniques des abonnés et s’adapter à la tendance de développement du marché. Les pièces structurelles en profilé d’aluminium extrudé présentent également d’autres avantages en répondant à certaines exigences strictes en matière de structure de véhicule. Par exemple, la rigidité de la structure d’extrusion de coque à double couche peut garantir que l’impact aérodynamique produit lorsque le train à grande vitesse se rencontre a une résistance particulière aux chocs. Une autre caractéristique importante de la carrosserie avec cette structure est sa grande rigidité longitudinale. Le rapport de rigidité longitudinale et transversale peut atteindre 70:30, tandis que le rapport de la carrosserie en acier est de 40:60. En outre, les profilés en aluminium peuvent également répondre aux exigences d’une bonne forme externe, sans l’utilisation de charges et beaucoup de travail manuel. Par exemple, pour certains modèles des chemins de fer fédéraux allemands, puisqu’aucune charge n’est utilisée, après calcul, avec le revêtement de peinture, le poids personnel peut être de 500 kg.
L’utilisation de pièces structurelles en profilé d’aluminium extrudé oblige également les constructeurs automobiles à faire face à des tâches complexes. Ils doivent trouver un équilibre entre les prix de la main-d’œuvre et des matériaux, et obliger les concepteurs à s’efforcer d’atteindre cet équilibre. Il convient de préciser que le matériau n’est qu’un facteur dans l’ensemble du concept. Le processus de production et le processus technique adoptés doivent également être formulés en détail pour être conformes à la capacité de production de l’entreprise et équilibrés avec l’investissement.
Par exemple, pour la plupart des entreprises de fabrication de machines, minimiser les réserves de moyens de production est une priorité absolue. Le choix des matériaux et des procédés par les concepteurs a un impact significatif sur cela. ABB dispose d’une ligne de production qui peut produire 8 véhicules avec carrosserie en aluminium chaque semaine, ce qui réduit le coût total du stockage des matériaux de 8%. Cependant, cet équilibre est facilement détruit en raison des changements dans le processus technique causés par l’utilisation de matériaux. Par exemple, lorsque le passage du soudage au collage nécessite plus de réserves journalières pour compenser le temps considérable requis pour le durcissement par collage.
Un autre fournisseur de premier plan de profilés en aluminium pour la fabrication de matériel roulant est la société allemande VAW. Les dirigeants de la société prévoient qu’il existe une grande tendance de développement dans la normalisation de la structure des véhicules et l’adoption de la méthode de conception de modules (cette tendance a été renforcée en raison de la demande du marché, elle a donc le soutien des fabricants), et estiment que compte tenu de la demande du marché pour la régionalisation du transport ferroviaire local en Allemagne, certaines entreprises privées accorderont plus d’attention à l’utilisation d’une structure de modules normalisée pour répondre davantage aux exigences des donneurs d’ordre individuels. À l’heure actuelle, divers constructeurs européens de locomotives et de véhicules ont un grand nombre d’idées de conception, et ces idées sont basées sur la conception de modules. Cette transformation vers la normalisation et la modularité est bénéfique à la fois pour les producteurs et les utilisateurs. L’expansion de l’utilisation de profilés en aluminium dans la fabrication de véhicules réduira considérablement le cycle de production en raison de l’utilisation plus large du soudage automatique.
Il est également évident que les véhicules à carrosserie en aluminium soudé ont une résistance élevée à la charge d’impact, ce qui est propice à l’amélioration de la sécurité de conduite. ABB a investi 1 million de livres pour organiser et effectuer le test de destruction de la structure en aluminium, et a obtenu des résultats satisfaisants et, plus important encore, les résultats attendus. L’entreprise a également accumulé une expérience pratique précieuse dans la réparation des méthodes de défaillance des véhicules accidentés. Au début de 1994, l’essai d’endommagement sur l’échantillon d’essai de voiture de tourisme à deux étages du train tgv-2n commandé par GEC Alstom en France a prouvé que lorsque la force d’impact était de 250 t, en raison de l’énergie d’impact absorbée de 8 mj, la structure a été extrudée pour un total de 80 cm et la carrosserie en aluminium est restée intacte dans son ensemble.
Dans le même temps, la reconnaissance des avantages de la carrosserie en aluminium n’est pas sans problèmes. Les constructeurs de locomotives et de véhicules à carrosserie en acier se sont dits préoccupés par l’accent mis sur l’aluminium dans le processus de fabrication des trains à glace en Allemagne et ont réalisé une étude pour confirmer la supériorité de l’acier en 1994. Cependant, comme auparavant, l’utilisation d’une structure en acier entraîne une augmentation d’environ 20% du poids mort de la carrosserie.
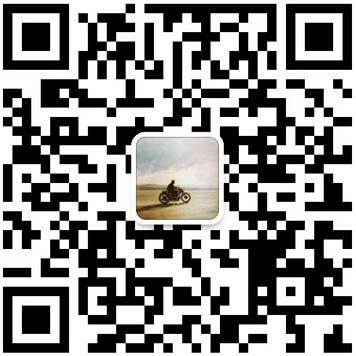
Offre gratuite de produits, bienvenue à consulter à tout moment, nous donnerons la première réponse. Notre e-mail: